Elevator pitch
A pieceworker receives a fixed rate for each unit (“piece”) produced or action performed. In part, the rate reflects a cost of monitoring output. A timeworker receives a fixed wage rate per hour that, in the short term, does not vary with output performance. From the 18th century up to the last third of the 20th century these were the two dominant payment methods in the manufacturing and production industries. Yet, today the incidence of piecework in advanced economies is very small, having lost considerable ground to time rates and to other forms of incentive pay. What caused this transformation, and has the movement away from piecework gone too far?
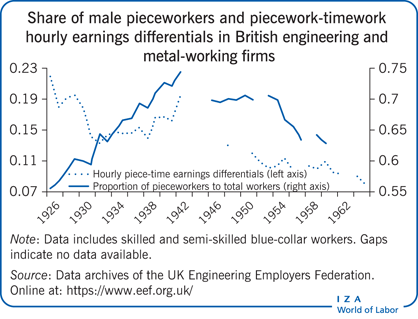
Key findings
Pros
Piecework is suited to low-output monitoring costs and long production runs.
Firms employing workers with wide variations in ability can benefit from piecework.
Piecework firms are more likely to retain their more able workers in tight labor markets.
Piecework pay is positively correlated with prevailing business conditions.
Piecework avoids subjective assessments of work performance.
Cons
Changes in product lines and technology increase the costs of setting and negotiating piece rates.
Output requiring joint inputs among workers is difficult to monitor and reward on an individual basis.
Piecework is not suited to manufacture that involves “hard-to-observe” process innovations.
Just-in-time production processes reduce the need for maximizing individual output.
Piecework discourages individuals from sharing insights into more efficient task executions.